Retailers: Hold fast to standards
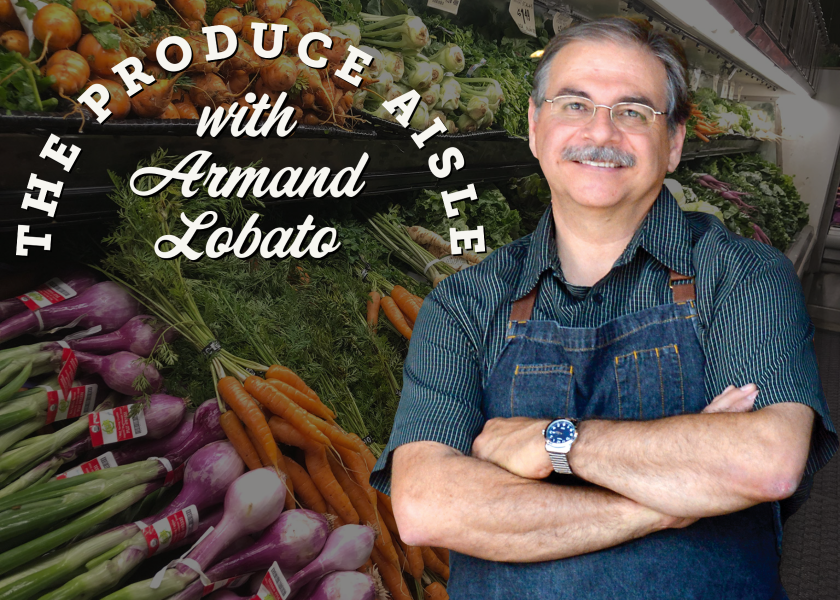
What stock condition is your store in? I mean, honestly?
I struck up a conversation with a woman on a recent trip and the conversation turned to the current, somewhat lethargic situation the country seems comfortable with now, when it comes to interrupted supply chains, taxed labor, etc. She commented that her husband was recovering from a stroke. While he was hospitalized in a major city facility, her husband received sub-par attention, she said, including infrequent check-ins, poor follow-up and lackluster sanitation.
She knew what she was talking about. She was a critical care nurse; her husband, a physician.
Standards exist for a reason. It’s what separates the bad from the mediocre, the fair from the good, the good from excellence. When I happened into a nearby grocer a few weeks ago, I was stunned. At 9:30 in the morning, the grocery shelves’ stock condition looked awful. The aisles were disorganized, many littered with opened and unopened cases scattered about on the floor, waiting to be stocked. Debris, half-worked carts and pallets were strewn about. The produce department was in poor shape, as well. At 2 in the morning, this would be expected, but mid-morning? With no obvious factors such as terrible weather?
Shoppers precariously maneuvered through the mess, amid just a handful of clerks with no sense of urgency. I couldn’t help but peek into the back dock area, where pallets of goods sat undisturbed.
Has it really come to this? Is this the new normal?
Here’s a thought: There was nothing wrong with the old normal, and the quicker we return to it, the better.
I’d like to think this store’s embarrassing stock condition was an exception. If a manager had to face his or her district manager walking into this disaster, they might scramble, citing perhaps late loads or multiple sick calls. But excuses only go so far.
The grocers (and produce departments) I’ve been privileged to be a part of over the years would also beg to differ. Applying the “when the going gets tough, the tough get going” mentality, stores should be as fully stocked as possible every day. Produce departments should have a clean, fresh wet rack set and ready by the time the store opens each morning. Dry tables should also be rotated and neatly stocked, with displays level, culled and detailed throughout the day. Customer service? That’s job one.
And throughout the stores, there should be minimal out-of-stocks.
If all this looks a little familiar, it should. I touched on the subject not long ago and it warrants extra emphasis. However, my concern is that complacency is creeping into some retailers’ mindsets — amid a sometimes-limited supply chain and strained labor situation — that resulting lower standards are somehow acceptable? A crutch to lean on? We see it across the board, including in retail home improvement stores and even in the health care example I mentioned at the start of this column.
I’ve been in plenty of stock condition dire straits; walking into messes as a clerk and, later, in my supervisor days. Sometimes, it’s a question of firing up the produce crew and identifying the hot spots.
Setting time and listing priorities. Instilling a sense of hustle into everyone as you work through a standards triage. That included yours truly. During store visits, I ditched my sport coat many times in understaffed situations for an apron, grabbed a cart, a trim knife and pitched in to help a crew catch up.
Sometimes, that’s all it takes. Retail managers, top to bottom, have to muster a little courage, show some leadership (that’s why you were promoted in the first place, right?), insist, even demand, that a store’s standards remain the priority. It’s about maintaining sales and gross profits in the moment, to be certain. But long term, it’s about expecting the best from everyone, every day.
As the former Green Bay Packers Head Coach Vince Lombardi said, “you don’t do things right once in a while, you do them right all the time. Winning is a habit. Unfortunately, so is losing.”
— Armand Lobato
Armand Lobato works for the Idaho Potato Commission. His 40 years of experience in the produce business span a range of foodservice and retail positions.